Does It Smelt? Re-Smelting Iron Scraps in a Shaft Furnace
- CBusuttil's Blog
- Log in to post comments
My colleague, Dr. Zech Jinks-Fredrick, and myself, Chris Busuttil, decided to embark on a project of discovery. Our project was designed as a control experiment to determine the feasibility of re-smelting iron scrap in a prehistoric furnace. This topic has been widely debated within the British archaeological community, especially in conversations regarding the motives of hoarding iron objects.
The project was not helped by the fact that we lived on opposite sides of the EU. To do an experiment would mean travelling and doing as much as we could on the short holiday together. Unfortunately, this led to logistical issues and not enough time was available to properly prepare the furnace.
Local mixed clay (peaty, estuarine clay with marine silts from the Hull valley) was sourced for the furnace. This clay seemed to have decent refractory properties and quickly vitrified once fired. However, the gravel present in the clay negatively impacted the structural integrity of the shaft’s walls. While the furnace did perform and a bloom was achieved, it would have been a greater success had there been more time to sieve the clay and allow the furnace to dry.
The furnace took 2 days to make, digging the clay directly from the ground and mixing it with water to make it more workable. Once the furnace was half finished, we built a small fire inside to dry it out. It didn't take long to start cracking but we pushed on and raised the furnace height on the 2nd day before lighting another fire inside it.
On the 3rd day the furnace was filled with hardwood charcoal sourced from CPL Ltd, and set alight. Alternating charges of scrap metal and charcoal were added once an adequate temperature was reached. We were somewhat put off by the addition of some rain to the mixture but luckily it soon cleared up (Figs 1 & 2).
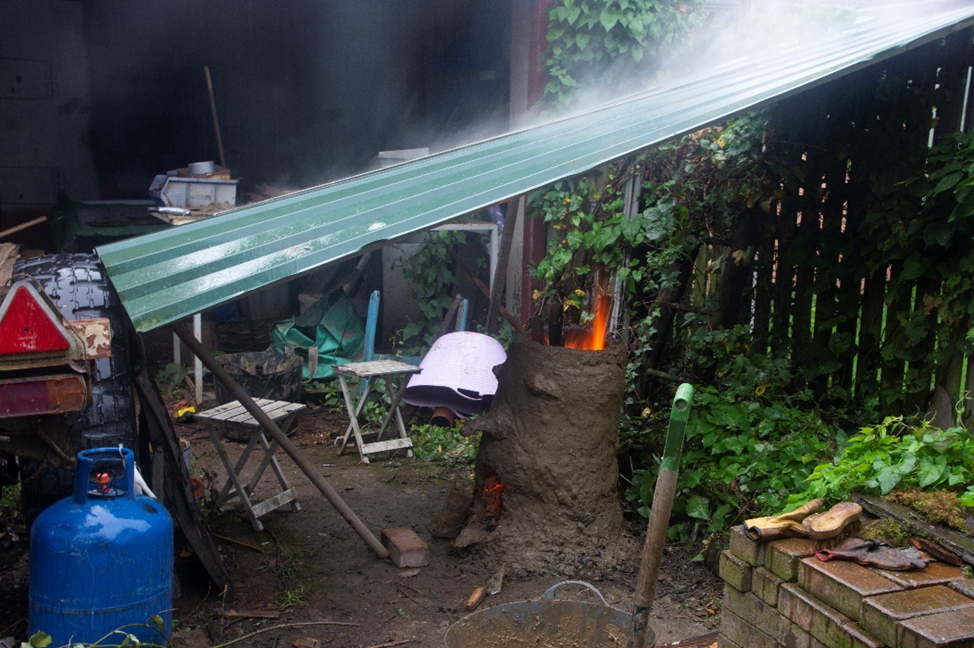
Fig. 1: Rain falling on furnace
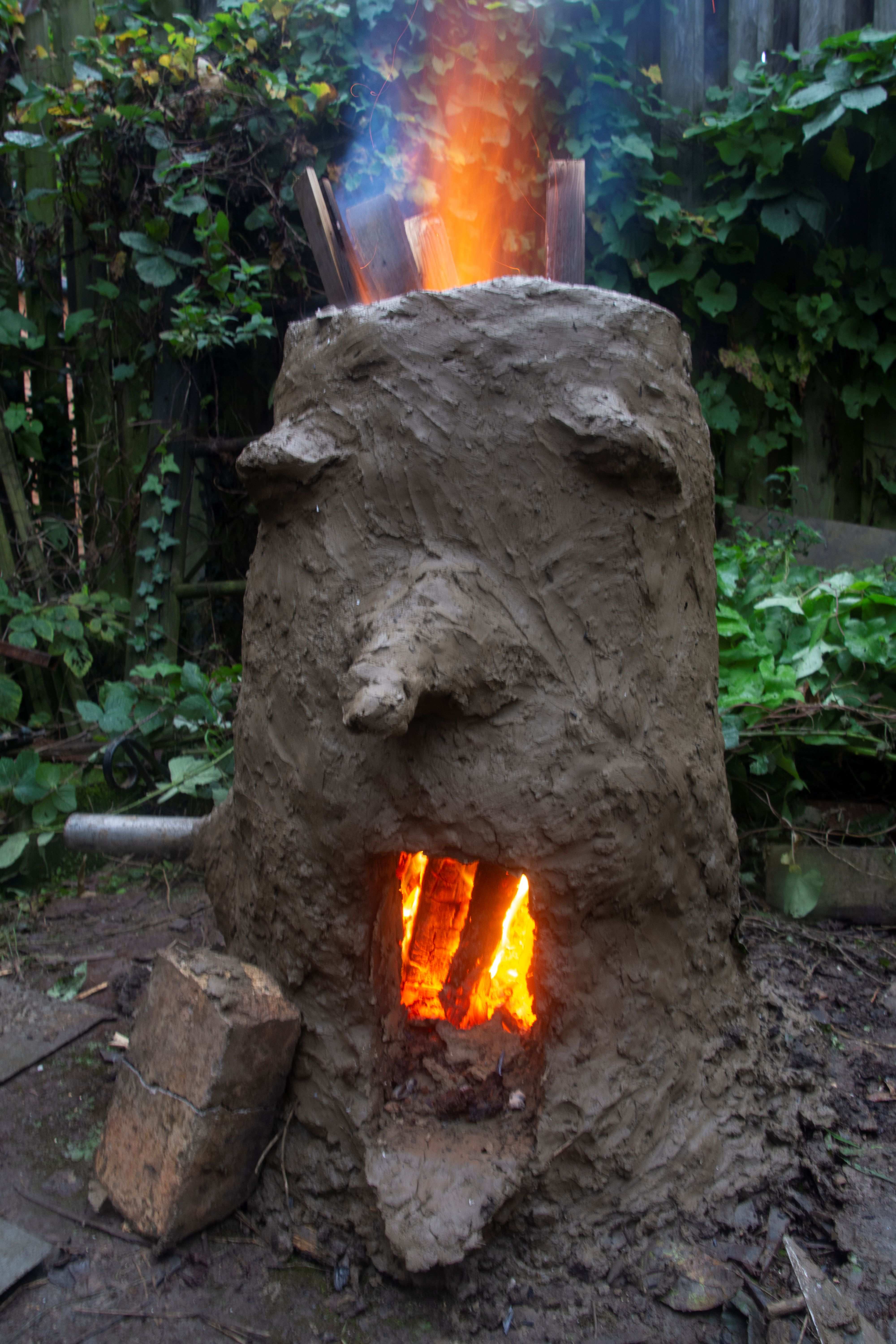
Fig 2: Drying the furnace from the inside
The scrap metal was sourced from the local smithy, The Anvil and Yew Ltd and included larger pieces of flashings, scarf remnants, and grinding dust. The steel material used had a slightly greater melting point (c. 1475-1495°C) than that of Iron Age iron or limonite (c. 1450°C), the ore commonly used for smelting in Iron Age Britain. While the material used is not directly comparable to the wrought iron (< 0.07% carbon by weight) or the low carbon heterogeneous steel (< 0.2% carbon by weight) primarily used before the introduction of blast furnaces (c. 12th century in Britain), it still provides valuable data. Specifically, if remnants of homogeneous modern steel could be smelted in an Iron Age shaft furnace, heterogeneous low carbon steel and iron scraps could most certainly be re-smelted in the Iron Age.
Due to time constraints the furnace was not left to dry long enough and repairs to the furnace were almost constant throughout the day. The cracking reached the inside of the furnace (Figs 3 & 4) and bits of furnace wall broke off bringing vitrified and non-vitrified contaminants into the bloom. The lining of the furnace also slumped off during the smelt and formed a shelf just above the tuyère, which not only vitrified and formed glass attached to the bloom, but also led to the overheating of the steel pipe used to line the tuyère. Traditionally a wooden pipe would have been used as the tuyère lining, which may have reduced overheating near the tuyère.
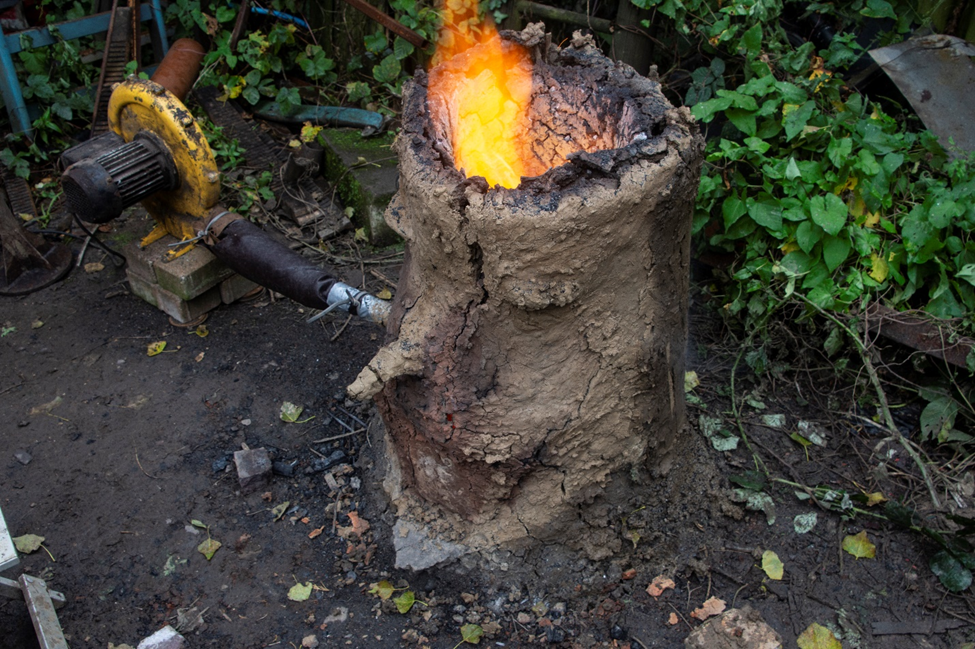
Fig 3: Severe cracking of the furnace both inside and out
Ceramic detritus from the collapsed shaft lining (Fig 4) contaminated the bloom (Fig 5) significantly making it more friable. Upon removal of the bloom this ultimately caused it to break into three large pieces. One of the less spongy and heavier pieces was cut down and prepared for microscopy (Fig 6).
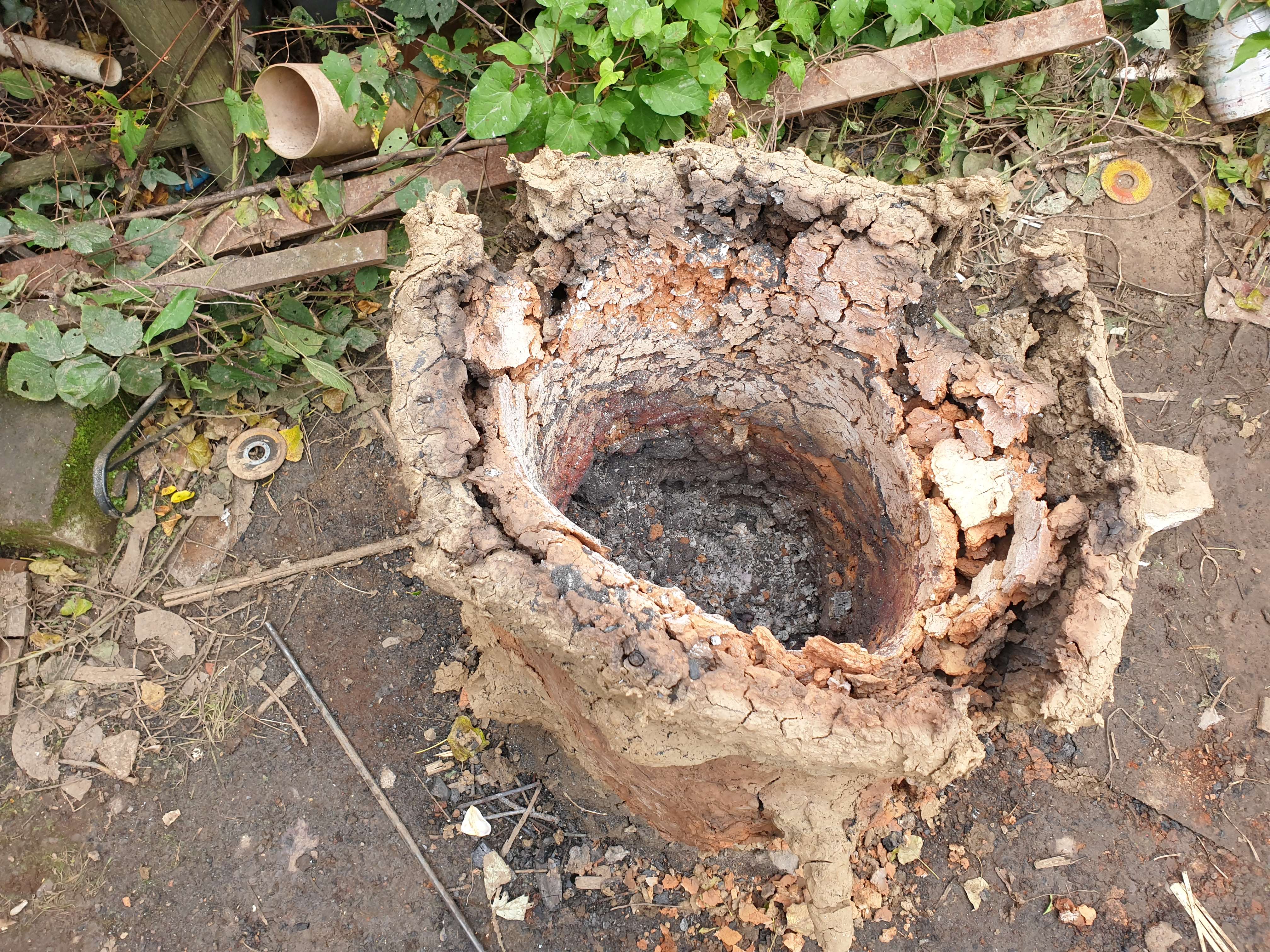
Fig 4: Ceramic bits missing from the furnace walls after the experiment was finished
An attempt was made to refine a small piece broken off from the bloom. This however proved difficult due to the large amount of glassy slag inclusions. Much of the larger pieces of scrap metal were only partially reduced and sticking out of the larger bloom. These should be able to be easily refined into the bloom in a bloomery hearth or chamfering type forge with ample heat (the core temperature needs to exceed 1250°C to facilitate a strong forge weld).
Fig 5: The bloom glowing inside the furnace
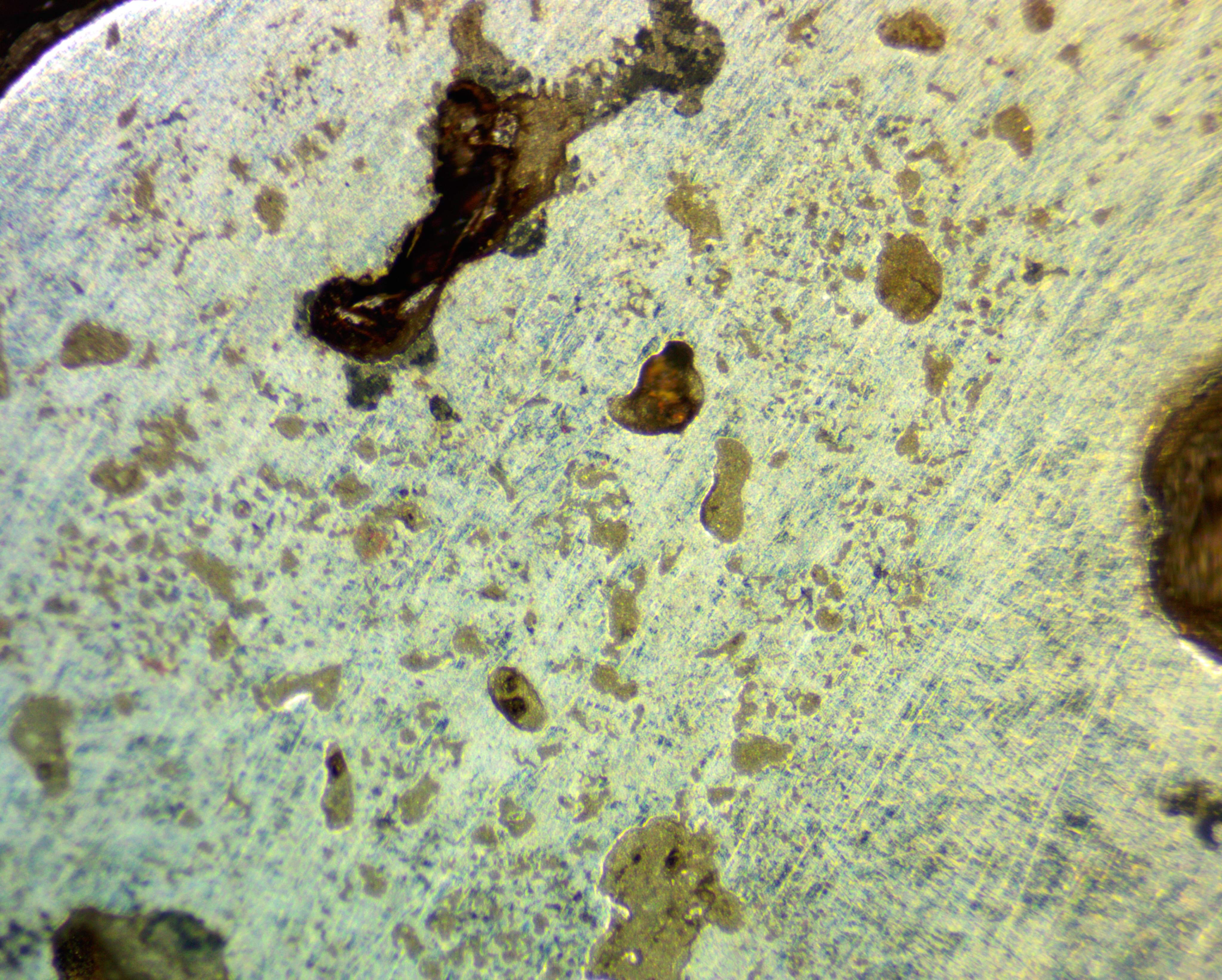
Fig 6: Bloom sample under a microscope at x100
As much of the iron provided was essentially dust, we were unsure how it should be added. The process of alternating a charge of steel sand and charcoal seemed to generate more heat however it seemed to disperse the bloom more into a lens rather than an ideally shaped football. In the future, making use of the ancient process of carburizing tools by wrapping them in leather and tallow may be a better approach for the smelting of grinding dust and scrap pieces. Thus potentially resulting in a purer and larger bloom.
In conclusion, the experiment was a success and brought to light several considerations. One of the most important factors to consider in future experiments is the furnace having ample time to dry. The re-smelting of iron and steel dust, scraps etcetera seems viable to Iron Age people of Europe. This realisation could greatly change the current understanding of hoarding what has long been described as iron scrap or detritus. In the modern era, we live in a world of waste, where it is often cheaper to buy new than remake something old. It is then important to recognise that people of the past would have gone to great lengths to reuse what might be considered waste in today's world. This raises another future research question, is the re-smelting of iron scrap worth the material and people hours when compared to a fresh smelt with bog ore? It is also noteworthy that no similar experiment has been conducted, at least not in academic literature.
Written by Chris Busuttil and Dr. Zech Jinks-Fredrick
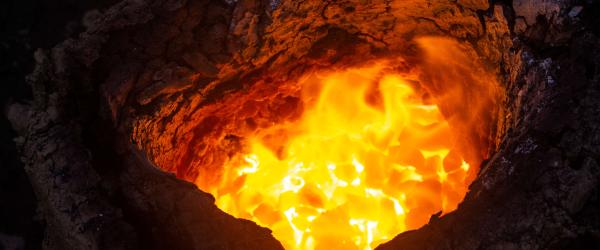